En cette année 2023, Frederique Constant fête ses 35 ans, ainsi que les 15 ans de son emblématique calibre tourbillon. Pour l’occasion, la maison dévoile une Classic Tourbillon Meteorite Manufacture en platine avec un cadran en météorite, limitée à seulement 35 exemplaires. Et c’est une première : chaque exemplaire est entièrement fini à la main. Un exercice confié à deux horlogers de la Manufacture chargés d’une seule mission : atteindre le plus haut degré de finition manuelle possible sur le mouvement.
Pour le public de collectionneurs, cette Classic Tourbillon Meteorite Manufacture représente, avec ses seulement 35 exemplaires faits main et numérotés, le collector ultime. La découpe de son cadran laisse apparaître, à 6h, le tourbillon Manufacture que Frederique Constant a créée il y a tout juste 15 ans, en 2008. Il s’agit ici de l’un des rares tourbillons qui s’offre en boîte en platine et cadran météorite actuellement disponible sur le marché.
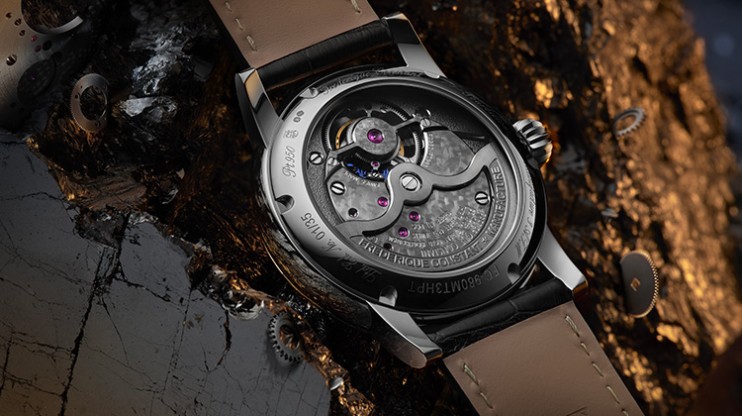
Mouvement : le summum de la finition manuelle
Pourtant, l’essentiel ne sera pas visible d’un distant regard. Il faudra un œil plus proche, mais aussi plus averti, pour déceler ce qui n’avait jamais été réalisé sur une montre Frederique Constant : la finition entièrement manuelle de la totalité des composants du mouvement. Un exercice unique, inédit, auquel se sont livrés deux horlogers spécialisés dans les mouvements Manufactures et à complication de la Maison.
C’est à l’aide d’instruments et d’outils traditionnels qu’ils ont effectué, à la main, et des semaines durant, le minutieux travail de finition de chaque composant : une lime cabron pour l’anglage, un marteau et un pointeau pour le martelage, du papier abrasif de seulement 9 microns utilisé sur le bâti (pont) et l’assiette de la cage du tourbillon afin de reproduire, par charbonnage, l’aspect du cadran météorite. Un seul pont exige à lui seul entre deux et trois jours de travail.
Perlage et étirage des flancs sont faits à la main, et l’intégralité des composants est décorée de chacun des côtés – même ceux que l’œil ne peut apercevoir. Mais pour ce qu’il peut discerner, Frederique Constant a œuvré au plus infime détail, à l’image des vis polies bloquées. Il s’agit ici d’une technique particulièrement ardue de polissage sur une plaque de zinc avec de la diamantine.
Une fois polies, le rendu des vis alterne de l’acier au noir en fonction de la lumière, créant un contraste toujours unique en fonction de l’exposition du mouvement. De ces vis, ce dernier en possède une quarantaine. Chacune d’elle exige environ 40 minutes pour être polie et anglée à la main. Une fois la pièce assemblée et terminée, le contrôle de chacun de ses composants s’effectue selon les plus hauts critères de qualité de la Haute Horlogerie. Cet exercice, qui place Frederique Constant au rang des ateliers indépendants, offre à la Manufacture un saut qualitatif de grande ampleur, qui pourra inspirer de futurs développements.
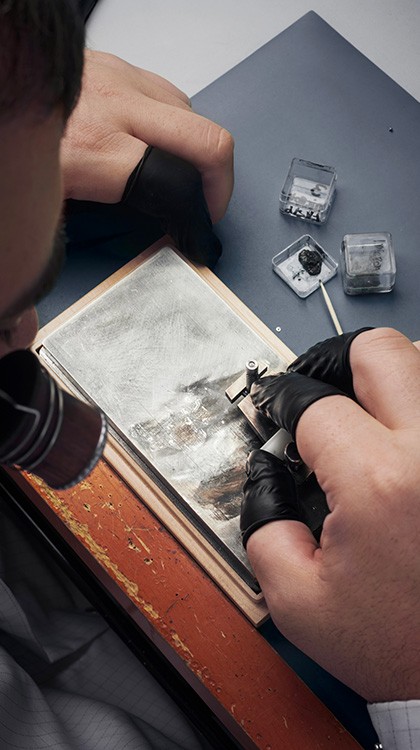
Cadran : 35 pièces véritablement uniques
Le cadran météorite est le précieux témoin d’un savoir-faire d’exception. Fragment d’espace tombé sur Terre par un heureux – mais rare – hasard, à Gibéon, en Namibie, il n’est pas meilleure illustration du rapport entre l’Homme, l’univers et l’astronomie, dont l’horlogerie est la fille directe. Mais ce morceau d’histoire céleste est aussi un morceau de bravoure : en termes de métiers d’art, ciseler un cadran en météorite, gorgé de métaux, est un exercice de haute voltige.
En effet, le précieux matériau se casse, s’effrite, et peut avoir subi (en raison de l’abondance de fer qui s’y trouve) de graves altérations, dont principalement la corrosion. Il faut donc une extrême dextérité pour découper un disque parfaitement plan, lisse, et dont aucun copeau ne s’échappera au détriment du mouvement qu’il recouvre. Le cadran météorite, de seulement 0,5 mm d’épaisseur, est à cette fin recouvert de ruthénium. Ce traitement sublime ses reflets naturels de gris et en préserve la surface de l’oxydation.
Mais l’exercice méritait sa peine : s’agissant d’une matière naturelle, chaque cadran à base de météorite sera différent des autres. Il n’y aura donc pas 35 pièces en série limitée, mais bel et bien 35 pièces uniques.
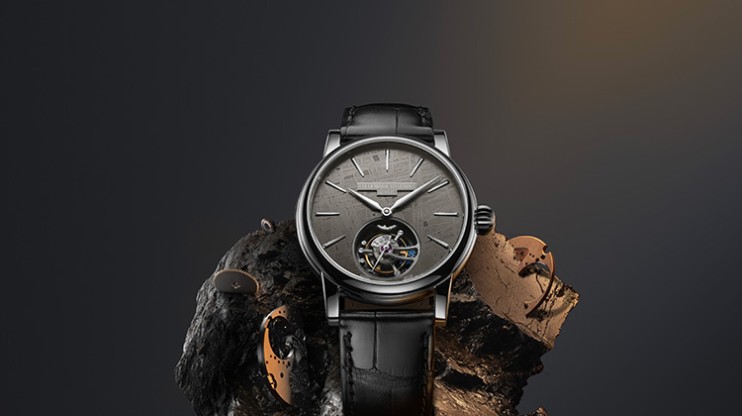
Une création harmonieuse
Pour garantir la cohérence visuelle avec la couleur du cadran météorite, le mouvement a également été traité en finition ruthénium, très rare chez Frederique Constant comme dans l’industrie horlogère, d’où son choix. Chaque gravure, dont le numéro individuel de la pièce (inscrit sur la cage de tourbillon et côté fond également) reste rhodiée dans sa profondeur, afin que les caractères ressortent avec un éclat plus vif. La masse oscillante est, quant à elle, constituée de laiton et d’une section en tungstène située sur son pourtour. Ce matériau a été sélectionné pour sa densité : supérieure à celle de l’or 18 carats, il induit une plus grande inertie lorsqu’il est en mouvement, permettant de réarmer plus rapidement le ressort de barillet. Toutes les parties de la masse oscillante sont également revêtues de ruthénium.
La Classic Tourbillon Meteorite Manufacture est présentée dans une boîte de 39 mm en platine. C’est la première fois de son histoire que Frederique Constant associe un cadran météorite avec ce précieux métal.
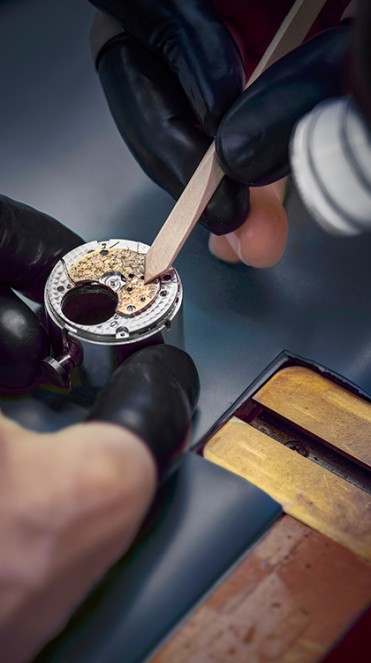
Le tourbillon Manufacture
Dévoilé en 2008, le mouvement tourbillon Manufacture FC-980 - développé en interne et doté d’une ancre et roue d’échappement en silicium - est visible côté fond et offre 38 heures de réserve de marche.
Donner vie à un tourbillon requiert une habileté horlogère certaine. Initialement conçu pour améliorer les performances chronométriques, il est désormais prisé pour sa chorégraphie mécanique, exécutée sur le devant de la scène pour le plus grand plaisir des spectateurs. Grâce à son architecture, le collectionneur a une vue imprenable sur sa roue d’échappement en lien avec la palette de l’ancre, le balancier virevoltant de droite à gauche et le spiral battant de manière concentrique. Une aiguille, positionnée au-dessus de la cage du tourbillon, indique l’écoulement des secondes.
Notons par ailleurs que Frederique Constant a été l’un des premiers à adopter le silicium pour ses nombreux avantages. La roue d’échappement et l’ancre en sont constituées. Ces parties aux reflets violets, combinées avec le reste de l’échappement, les organes de régulation et la cage du tourbillon, ne pèsent que 0,59 gramme, d’où une très faible consommation d’énergie pour être mise en mouvement.